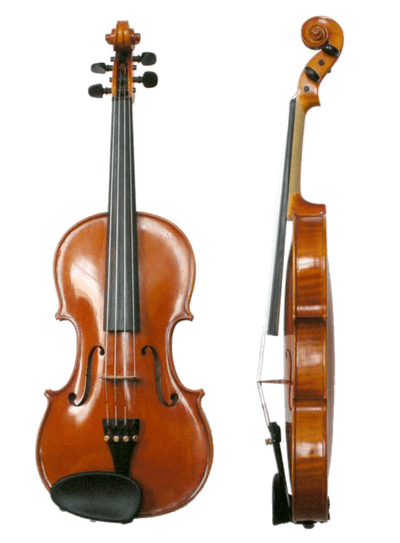
Solacure understands the needs of violin and other instrument makers. We were the first to offer kits specifically for curing/drying violins, and we are the sole vendor for International Violin, for their customers. Our system is far superior to any alternative, and can dry any linseed oil based finish in one day, instead of two weeks. They also "tan" the wood, making it look warmer and more inviting to the musician. More importantly, if you don't like our kit, ship it back for a full refund during the first 30 days. No fine print.
We have a few options for violin makers, including our standard kit in 4 or 6 foot length (for double bass and cello), as well as a simplified kit for luthiers who don't want to wire anything up. It has four specially wired F64 fixtures that you just set up, plug in and go. Our standard kits have most everything you need, but you will need two things that you can buy locally or on Amazon. Below is a brief overview.
Overview
To use the kit, you are going to need a few more things. You will need to build a box to house the light. Outside dimensions of 28" x 28" with a height of over 48", or a little bigger if you do violas as well. The key is allowing 2" for the depth of the lamp and holders, plus keeping the lamps at least 4 inches away from the violin. The box should be open at the bottom to allow plenty of airflow and on the top it should have a fan that is blowing up. The fan doesn't need to be huge but it can't be tiny either. There are 100 ways to do this, depending on skills and budget. The idea is to work with the natural convection and just exhaust the excess heat.
The majority of builders use a small motor to spin the violin in the chamber slowly. The most common source for this is the motors used for mirrored balls (disco balls) that night clubs use. Any DJ supply house should have them. They rotate around 6 revolutions per minute, which is perfect. They are fairly inexpensive. A few people have modified the motors from the rotisserie attachments from outdoor grills. This is a little overkill, but if you have access to one already, it will work. The key is slowly turning the violin so it will get even exposure from the lights.
The ballast that powers the bulbs should be connected on the OUTSIDE of the box, so we aren't adding unnecessary heat to the box. Assuming you are building a wooden box (the vast majority do) then you can screw the ballast directly to the outside. The ballast is connected with two screws. We strongly suggest using long enough screws that you can stick a bolt through the screw, kind of like a washer, between the ballast and the wood. This shim will raise the ballast off the wood surface and help keep it cool. 1/4" to 1/2" is sufficient to prevent heat from building up in the ballast. It isn't required, but since you will be running the ballast for days at a time, it is a simple way to extend the life of the ballast.
Depending on where you live, a humidifier may be a good idea. A small to medium sized humidifier that puts out near the base of the violin rig is helpful to keep the wood from drying out during the curing process, particularly if you live in a dry area, or it is very cold outside, thus the indoor air is already dry. We want to pace the curing process, not rush it, and we want to be sure to not overdry the wood, so for less than 50 dollars, it's good investment.
You want to buy a can of spray glue (3M makes a good product for around 7 bucks at any hardware store). You will spray the inside and cover the inside with aluminum foil. making sure the shiny side faces in. This does not need to look perfect, and in fact, it is better if the foil is NOT perfect, as to make the light diffuse better. This isn't a required step, but it is beneficial and cheap. You will need to have a parabola or at least a flat surface that doesn't interfere with airflow on the bottom of the box. This doesn't need to be attached, it can be something you put in place once you get started curing. The idea is to reflect some light onto the bottom of the violin, which isn't being directly exposed.
Some luthiers (mainly cello builders) will opt to add a 24" bulb and fixture to better cover the end of the cello. We have these, and you can use this 24" light regardless of which kit you are using as a primary means to cure/dry your instruments. The fixtures just plugs into any wall sockets; no special wiring needed. You can buy the bulbs individual, or buy one bulb and fixture at a great price.
Once built, your rig should last a lifetime. Most people will replace the lamps once they notice the finish isn't drying as fast as it once was. This depends on how many violins you finish, so it might mean once every 5 years, or once a year. The lamps don't "go bad" very quickly, so even 10 year old lights should be fine, it is all about usage, not age. The ballasts and other parts should last for decades.
All our luthier kits use the SG-1 series lamps, which have a touch of green phosphor to make them easier and safer to work with, and come with UV glasses.
We have a few options for violin makers, including our standard kit in 4 or 6 foot length (for double bass and cello), as well as a simplified kit for luthiers who don't want to wire anything up. It has four specially wired F64 fixtures that you just set up, plug in and go. Our standard kits have most everything you need, but you will need two things that you can buy locally or on Amazon. Below is a brief overview.
Overview
To use the kit, you are going to need a few more things. You will need to build a box to house the light. Outside dimensions of 28" x 28" with a height of over 48", or a little bigger if you do violas as well. The key is allowing 2" for the depth of the lamp and holders, plus keeping the lamps at least 4 inches away from the violin. The box should be open at the bottom to allow plenty of airflow and on the top it should have a fan that is blowing up. The fan doesn't need to be huge but it can't be tiny either. There are 100 ways to do this, depending on skills and budget. The idea is to work with the natural convection and just exhaust the excess heat.
The majority of builders use a small motor to spin the violin in the chamber slowly. The most common source for this is the motors used for mirrored balls (disco balls) that night clubs use. Any DJ supply house should have them. They rotate around 6 revolutions per minute, which is perfect. They are fairly inexpensive. A few people have modified the motors from the rotisserie attachments from outdoor grills. This is a little overkill, but if you have access to one already, it will work. The key is slowly turning the violin so it will get even exposure from the lights.
The ballast that powers the bulbs should be connected on the OUTSIDE of the box, so we aren't adding unnecessary heat to the box. Assuming you are building a wooden box (the vast majority do) then you can screw the ballast directly to the outside. The ballast is connected with two screws. We strongly suggest using long enough screws that you can stick a bolt through the screw, kind of like a washer, between the ballast and the wood. This shim will raise the ballast off the wood surface and help keep it cool. 1/4" to 1/2" is sufficient to prevent heat from building up in the ballast. It isn't required, but since you will be running the ballast for days at a time, it is a simple way to extend the life of the ballast.
Depending on where you live, a humidifier may be a good idea. A small to medium sized humidifier that puts out near the base of the violin rig is helpful to keep the wood from drying out during the curing process, particularly if you live in a dry area, or it is very cold outside, thus the indoor air is already dry. We want to pace the curing process, not rush it, and we want to be sure to not overdry the wood, so for less than 50 dollars, it's good investment.
You want to buy a can of spray glue (3M makes a good product for around 7 bucks at any hardware store). You will spray the inside and cover the inside with aluminum foil. making sure the shiny side faces in. This does not need to look perfect, and in fact, it is better if the foil is NOT perfect, as to make the light diffuse better. This isn't a required step, but it is beneficial and cheap. You will need to have a parabola or at least a flat surface that doesn't interfere with airflow on the bottom of the box. This doesn't need to be attached, it can be something you put in place once you get started curing. The idea is to reflect some light onto the bottom of the violin, which isn't being directly exposed.
Some luthiers (mainly cello builders) will opt to add a 24" bulb and fixture to better cover the end of the cello. We have these, and you can use this 24" light regardless of which kit you are using as a primary means to cure/dry your instruments. The fixtures just plugs into any wall sockets; no special wiring needed. You can buy the bulbs individual, or buy one bulb and fixture at a great price.
Once built, your rig should last a lifetime. Most people will replace the lamps once they notice the finish isn't drying as fast as it once was. This depends on how many violins you finish, so it might mean once every 5 years, or once a year. The lamps don't "go bad" very quickly, so even 10 year old lights should be fine, it is all about usage, not age. The ballasts and other parts should last for decades.
All our luthier kits use the SG-1 series lamps, which have a touch of green phosphor to make them easier and safer to work with, and come with UV glasses.
![]() Regular price: $366.00 Sale price: $303.86 | ![]() Regular price: $492.00 Sale price: $399.96 | ![]() Regular price: $199.99 Sale price: $134.98 |
![]() | ![]() | ![]() |
Solacure Means Quality Solacure ultraviolet lamps aren't just good, we guarantee they are the best or we will give you your money back. Our patented glass is more transparent to UVA and UVB. Our custom cathode/anode sets lets you run 2 to 3 times more power than a standard lamp in the same size. All of our lamps have built in reflectors. We have a lamp for every need. We stand behind everything we sell and guarantee each will perform exactly to specification, or we will replace them. We don't want your business this week, we want it every week, and we are willing to earn it. There really is a difference in quality when it comes to ultraviolet bulbs, and Solacure tops the list. Order online, over the phone, or call us if you need a custom UV lamp made, with fairly low minimums (around 2000 pieces). We can make it happen. Buy with confidence: We like what we do, and we've been doing it for over 30 years. |
![]() Got a question? The best way is usually to email us at sales@solacure.com. |